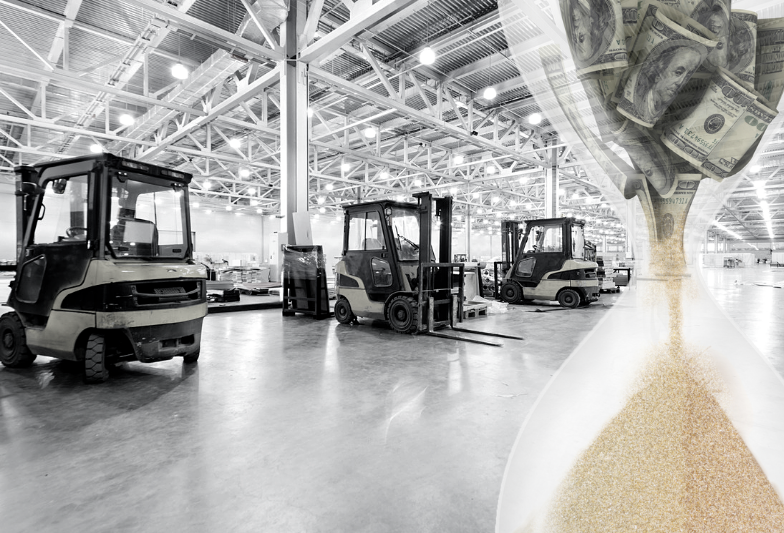
Imagine you have two identical pairs of jeans hanging in your closet. You wear one pair 6 days a week. The other, you only wear 1 day a week.
Naturally, the pair of jeans you wear most often begins to wear out. The waist stretches out a bit and the knees begin to tear. Frustrated, you patch up the knees and add a couple of stitches, but… you continue to wear making regular repairs all while wondering is something wrong with that particular jean.
Are you the problem, or are the jeans?
You guessed it — the jeans aren’t causing the issue. It’s you. The same scenario applies to vehicles in your fleet.
When a particular fleet vehicle is utilized more than others, it’s bound to need repairs faster. After constantly investing money into the vehicle, you get frustrated because it seems like it’s always breaking down, incurring expenses and resulting in downtime.
But the vehicle may not be the problem. We hate to break it to you, but just like the jeans, it may be you who is causing the issue.
Why 10,000 Hours is the Magic Number
Here’s the thing, fleet vehicles aren’t meant to last forever. That’s why it’s critical to track how long each vehicle runs. This way, you know if they are reaching their “expiry”.
The amount of time most fleet vehicles are expected to run properly without major issues is 10,000 hours.
Meaning if you have a vehicle running over that amount, it may not be worth it to continue repairing it. Similarly, if a vehicle has run lower than that amount, it may not be worth it to replace it just yet.
One of our clients, PITCO, was considering a brand new lease on its material handling equipment. When we ran the numbers, it turned out many of the vehicles had only 300 hours on them — with the average usage being 2,300 hours. This was barely a fraction of the 12,000 hour total lifespan of those vehicles.
We were able to save PITCO $450,000 over 5 years by recommending a combination of new and used equipment instead of replacing the whole fleet.
Plan When to Replace Equipment
When you’re tracking how much usage vehicles are getting, you’re able to see trends and make realistic plans.
If one truck is used around 1,000 hours each year, for example, then you know that it will take approximately 10 years to reach the 10,000 hour lifespan of that truck. You can then plan for the expense of a new fleet vehicle in year 10 because you can reasonably expect for it to break down that year.
Similarly, if you see that in the 5th year, the truck begins to need constant repairs, you can investigate the situation. Instead of replacing the truck in its 5th year, it may be wiser to figure out why it’s breaking down so much then. It could be an issue with
- Usage
- Type of part breaking down
- Repairs
- Route taken
There are many factors to consider before deciding to replace a vehicle, especially if it has been driven considerably less than 10,000 hours.
Avoid Wasting Resources
Once a vehicle reaches the point of “beyond useful life”, it’s time to figure out next steps. If you don’t know hours worked, precious resources repairing and servicing could be wasted.
Imagine a vehicle over 12,000 hours needed a battery replacement each year. Instead of spending that money, you may be able to actually save on your overall operating costs by replacing that vehicle entirely. However, if you have no idea how many hours a vehicle has run, you don’t have the insight to make that decision.
Although, don’t assume when vehicles continuously break down, it’s time for them to be replaced. Knowing how long vehicles run is key.
It’s not credible to estimate the run time on a vehicle. It should be tracked accurately to avoid wasting resources on replacement or repairs.
Don’t Blow Your Budget
Knowing when to service or replace units is like a superpower for a warehouse manager. This helps to run the fleet more efficiently, taking into account expenses and downtime. Knowing the run time on your vehicles can help maintain your budget for the long term.
This metric also helps you figure out how to best manage units at multiple locations.
Take two warehouses, for example. One has vehicles that have run 9,000 hours, while the other has vehicles that have run 2,000 hours, you may be able to delay replacing the vehicles by changing locations.
If one warehouse has less vehicle traffic, it makes more sense to utilize the vehicles that have a higher amount of hours there. This can help manage costs more efficiently, and provide a few extra months or years before needing to replace the vehicles.
Consider These Other Metrics Before Replacing Your Vehicles
Knowing which vehicles have run over 10,000 hours is a critical metric every warehouse manager should be tracking. However, it can be time consuming to track and update.
That’s where we can help.
With our 10+ years of fleet management experience, we have the tools and resources to track vehicles and help analyze your results.
In addition to vehicles that have run over 10,000 hours, did you know there are 4 additional warehouse performance metrics that can give unprecedented insight into your fleet?
We share those metrics in our 5 Key Performance Metrics On-Demand Webinar. Not only that, we provide the tools to run actual numbers and implement them into your warehouse. SIgn up for the webinar and get a free workbook and cheat sheet to help you get tracking.
Want to know how vehicle run time can change the way you manage your warehouse? Get in touch with us at 844-360-8217 or book a no-obligation consultation to get started.
Interested in one of our products? Give us a call at 844-360-8217 or click below to get started with a free quote now!