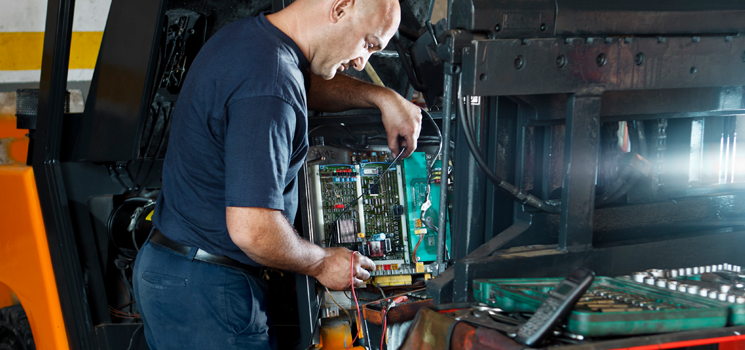
The more frequently you service your material handling equipment, the longer that equipment will last. Whether you’re a facility manager or warehouse owner, this type of regular servicing is simply good business.
But did you know that proper maintenance of forklifts and other industrial machinery is often a prerequisite for keeping the manufacturer’s warranty valid?
Fortunately, most manufacturers publish recommended servicing schedules for their products. After extensive rigorous testing, they already know the longest acceptable intervals required to ensure their material handling equipment remains in optimal working order.
Follow these recommended schedules, and you should be fine.
But if you fall behind on regular checkups and maintenance, you run the risk of letting your warranty coverage lapse.
And it only gets worse from there:
- Future breakages and downtime will happen more frequently.
- Necessary repairs won’t be covered and must be paid out of pocket.
- Those repairs will often be more extensive and expensive.
- Your material handling equipment will enjoy shorter useful lifespans.
And for heavier machinery, infrequent servicing may actually pose unnecessary health and safety risks for your teams.
The Benefits of Operational Maintenance with PMHSI
Following the manufacturer’s service schedule is always a good idea. But simply adhering to these guidelines isn’t enough. To keep the warranty coverage valid, you must also be able to document the frequency of all previous servicing.
However, staying on top of operational maintenance isn’t always easy. This is especially true if you manage a lot of material handling machinery.
This is why many companies outsource the job to mechanics their service requirements.
But at Pacific Material Handling Solutions (PMHSI), we employ journeyman technicians to perform operational maintenance – from top to bottom. This approach ensures your equipment receives the same cleaning and lubricating benefits you’d expect from a traditional mechanic. But your machinery also receives the detailed servicing, inspections, and diagnostics that only more qualified journeyman technicians can provide.
As a result, your material handling equipment benefits from:
- Longer lifespans and warranty coverage.
- Fewer breakages and equipment failures.
- Less downtime and lost productivity.
- Lower long-term and operating costs.
The following chart gives you an idea of how thorough our maintenance checklists are.
Level 1 Checklist Sample
Operational Maintenance and Documentation for Every Make and Model
We specialize in operational maintenance for a broad range of material handling equipment and components manufactured by industry titans like Cat, Hyster, Toyota, Crown, and Raymond. However, we understand the individual servicing schedules and requirements for nearly every major brand, make, and model. And if you prefer, we can come even more frequently than recommended, whether you need us every week, every month, or every 113 days.
It’s entirely up to you.
Most important of all, we can provide you with the requisite documentation to ensure your warranty coverage remains intact for as long as possible. Our technicians can even provide both hardcopies and digitally scanned backups so that you always have the documentation you need – when you need it.
To learn more about our comprehensive operational maintenance services, contact us today for a free consultation.