The proof is in the numbers. Here's how we've helped our customers increase productivity and decrease downtime.
The proof is in the numbers.Over the last decade, we’ve had the opportunity to work with clients from a range of industries. While their businesses may be different, our clients are looking for the same thing: higher productivity and lower downtime.
With the help of our highly experienced team at PMHSI, we enable our clients to reach their targets head on.
Whether they’ve outgrown their current equipment and need a new solution or they’re dealing with inaccurate repairs and service, we’re able to provide them with actionable solutions based on hard data — and our years of experience.
We’re proud to share in the successes of our clients. Read the case studies below to learn more about what kinds of results PMHSI can help your business achieve.
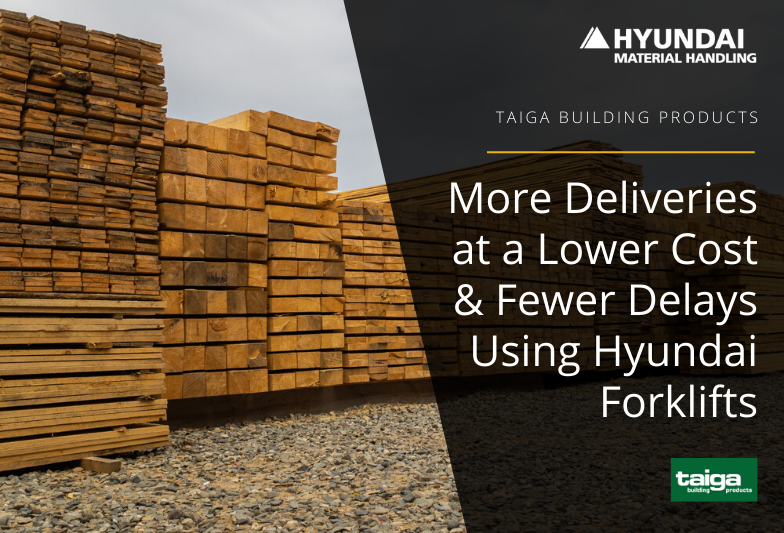
Taiga Building Products
Taiga is a leading provider of premium lumber, recycled construction materials, and other sustainable building products throughout North America. See how the company was able to acquire more productive forklifts and expand its fleet considerably.
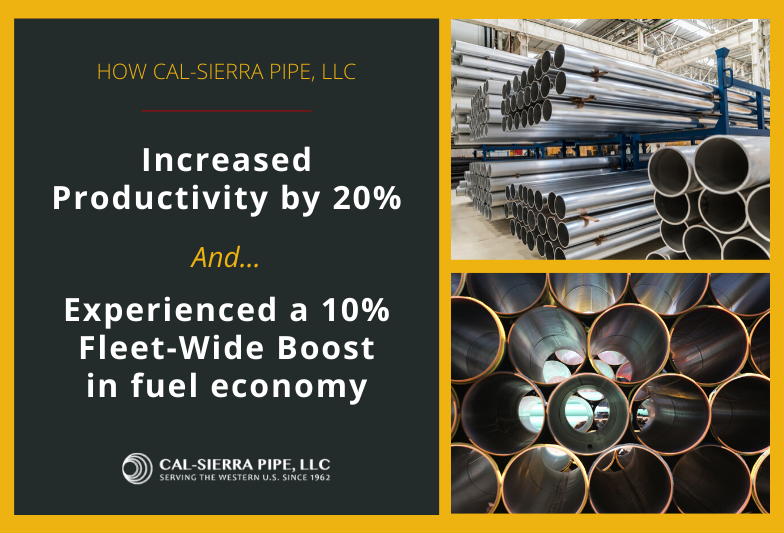
Cal-Sierra Pipe
For nearly 60 years, Cal-Sierra Pipe has been the “supplier of choice” for steel pipes and other industrial components throughout the construction, manufacturing and farming sectors. See how the company experienced a 10% fleet-wide boost in fuel economy.
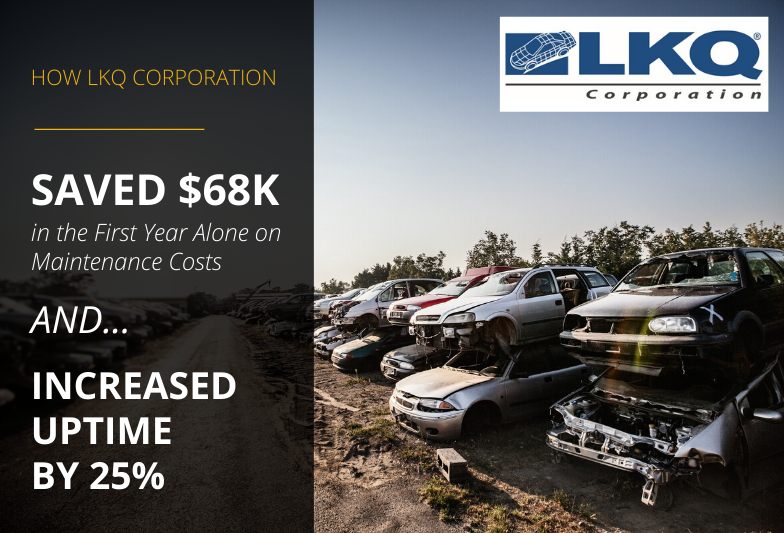
LKQ Corporation
LKQ is a leading provider of aftermarket collision replacement parts, recycled OEM components and other refurbished automotive repair products. See how the company saved $68K in the first year alone while increasing uptime by 25%.
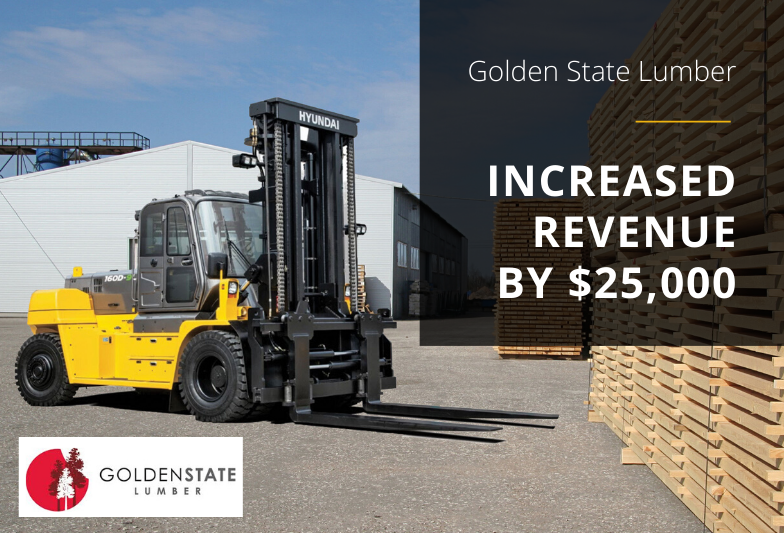
Golden State Lumber
Golden State Lumber opened in 1954 and is now the premier Northern California supplier of building materials. Learn how they increased productivity & increased their revenue by $25,000.
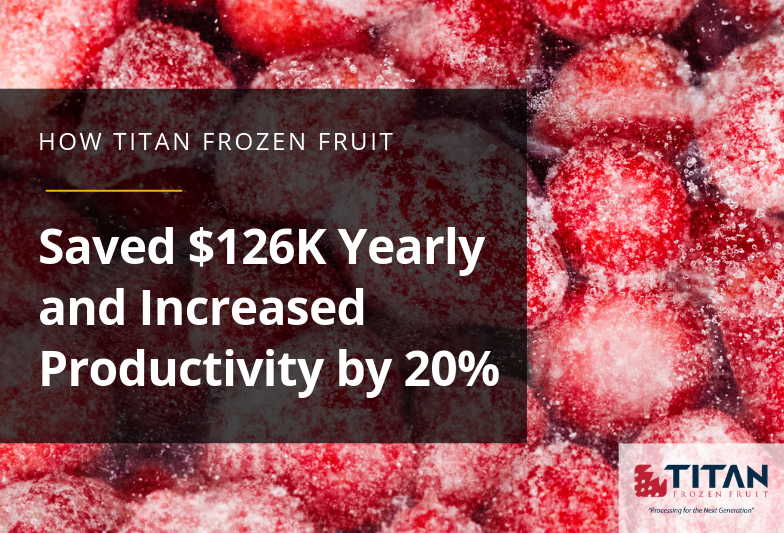
Titan Frozen Fruit
Titan Frozen Fruit is a strawberry processor, with operations in Salinas and Santa Maria, California. Learn how it increased warehouse productivity by 20% and how the company saves $126,000 annually.
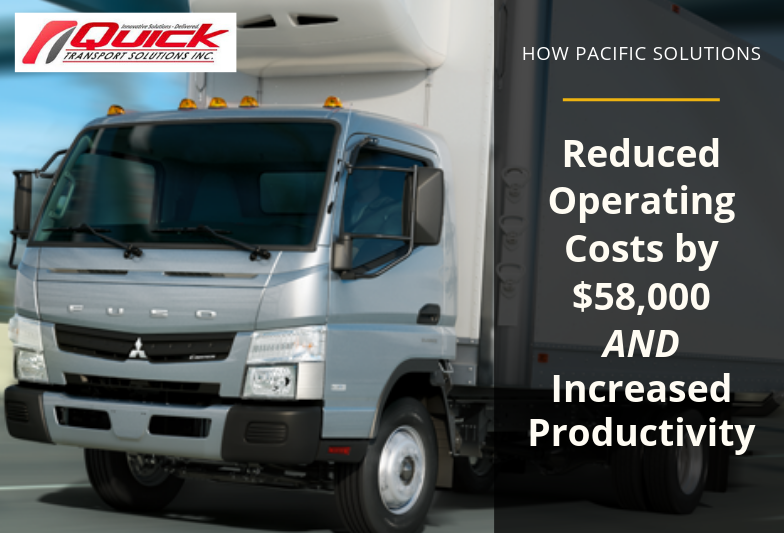
EZ 2 Build Express
EZ 2 Build Express is a logistics company with operations in California, Oregon and Washington. Learn how we reduced operating costs by $58,000 per year.
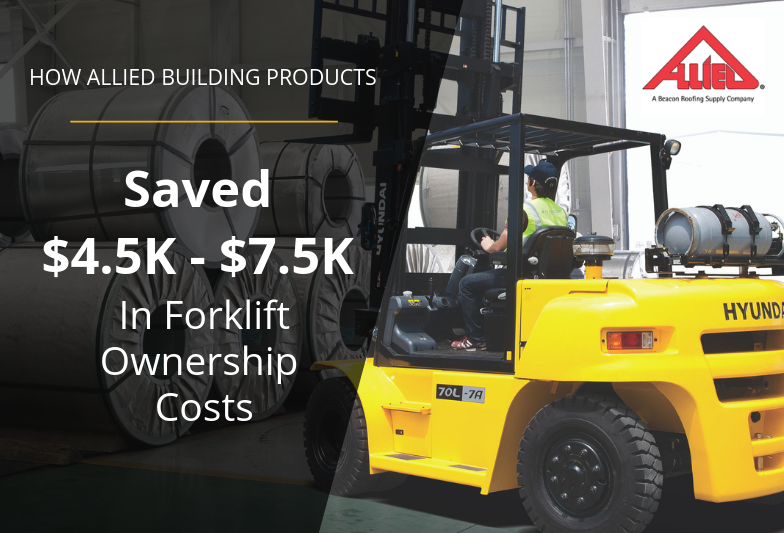
Allied Building Products
Allied Building Products is a roofing and building materials wholesale distributor with multiple locations throughout the United States. Learn how we saved $4,500 - $7,500 in ownership costs.
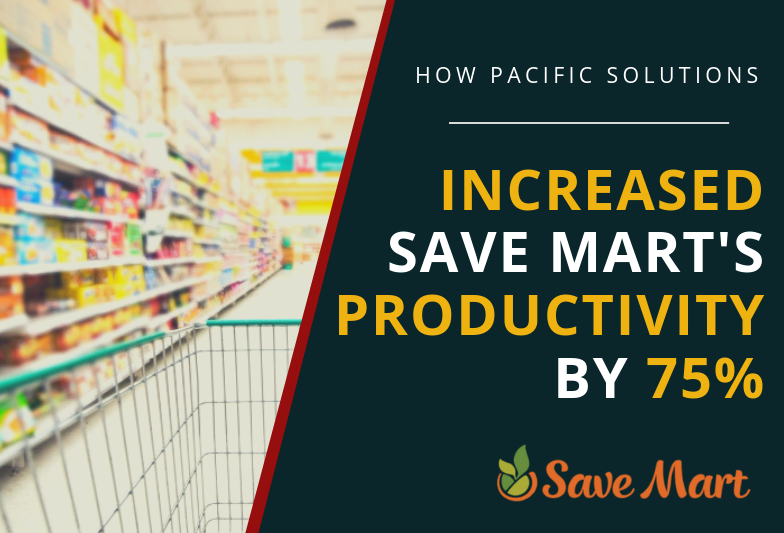
Save Mart
Save Mart is the largest privately owned grocery store chain in Northern California and Northern Nevada operating 208 stores and 2 distribution centers and needed a centralized way to manage their large fleet over a vast number of stores.
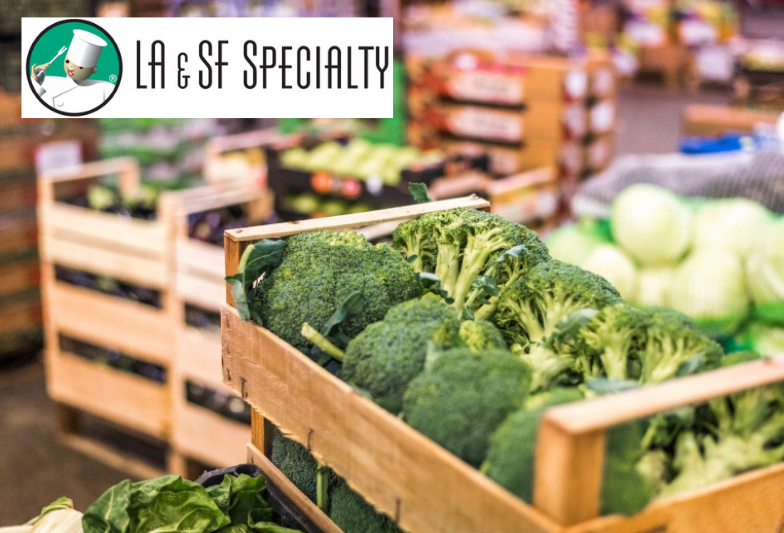
San Francisco Specialty
San Francisco Speciality is a wholesale distributor of fresh produce, meat, and high-end ingredients, with operations in East Bay and Los Angeles. Learn how we lowered annual maintenance costs by $24,000 for this wholesale distributor.
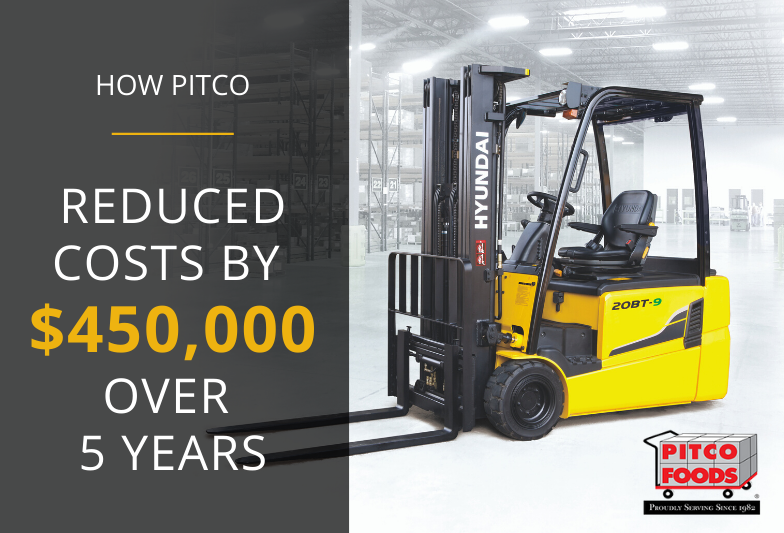
PITCO
PITCO is a leading wholesale distributor in California, focusing on independent stores, covering a large territory from Napa Valley to Fresno. Find out how we helped PITCO save over $450,000 in equipment costs over 5 years.