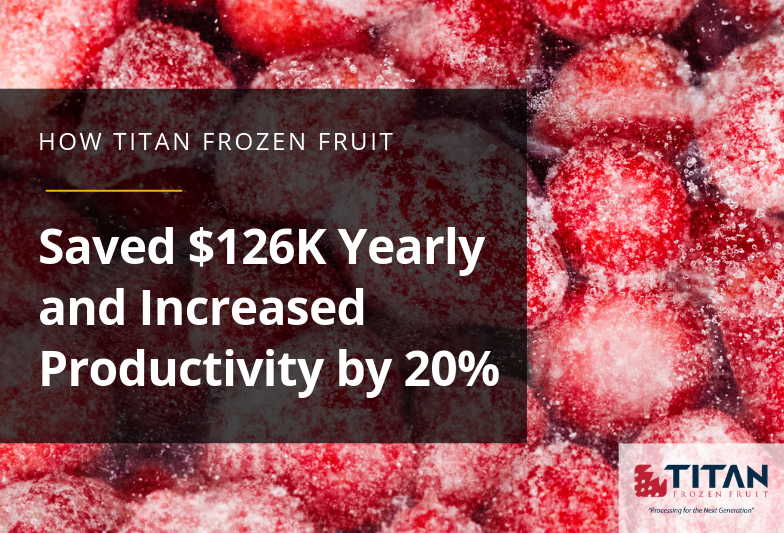
About Titan Frozen Fruit
Titan Frozen Fruit is a strawberry processor, with operations in Salinas and Santa Maria, California. Its operations include multiple shifts requiring forklifts to run longer-than-average hours.
As a result, their material-handling fleet needs to be efficient and powerful so it can match the extensive operational schedule.
The Problem
- Titan had transitioned to using electric forklifts from LPG due to concerns for their employees having to inhale exhaust fumes
- When combining the longer run times with electric forklifts, battery performance was critical to meeting their productivity goals
But…
- Due to their high hours of operation, Titan was utilizing 2 conventional batteries per forklift
- Using 2 batteries meant charging 1 battery while utilizing the other in the forklift, and changing the batteries at least once a day
- Battery exchanging, charging and watering reduced their productivity and increased the risk of accidents — which lead to Workers’ Compensation claims, higher costs and additional hiring and training expenses
The Solution
- After a thorough analysis, PMHSI recommended replacing the conventional batteries with lithium batteries and charges
- Lithium batteries require no watering and no extra batteries to change in and out
- Recharging the batteries could be easily done during breaks and lunch hours
- This short time to recharge provides 100% utilization of the equipment
The Result
- Thanks to this new lithium battery solution, Titan increased warehouse productivity by 20%
- They also required one less forklift and operator, saving the company $126,000 annually
- Titan could also ensure a better safety environment for their warehouse team, reducing their Workers’ Compensation claims exposure by 100%
It Can Work For You Too!
Are you a good candidate for lithium batteries? Take our short survey to see if your warehouse can benefit from this productivity-boosting solution.