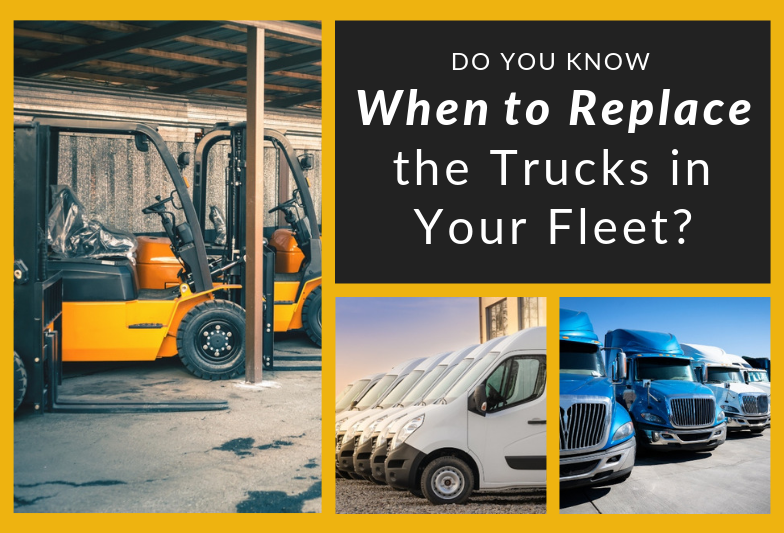
How does your organization decide when to replace the trucks in your fleet? Do you have a secret formula?
Figuring out how to get the biggest return on your investment is an important task. After all, you don’t want to replace your vehicle too early if a simple repair can give it a few more years of life. Similarly, you don’t want to replace your truck too late — repair and maintenance costs can add up, and it may be more cost-effective to purchase or lease a new vehicle.
Timing your vehicle replacement is key. The point at which it makes most financial sense to replace your vehicle is called the optimal vehicle lifecycle point.
Important Factors to Consider When Replacing Your Fleet Vehicle
A number of critical internal and external factors are needed to analyze when deciding whether or not to replace your trucks. Internal factors relate to your vehicle specifically:
- How many miles it has been driven
- How long it has been in service
- How often it is used
Essentially, the internal factors look at how much each vehicle is utilized during a specific amount of time. This is also called unit utilization.
While unit utilization is unique to each vehicle, there is also an external factor that affects your return on investment: how much you spend on repairing your vehicle.
Many businesses work with fleet repair services who are specifically contracted to maintain, service and repair the vehicles when they break down. Not all organizations provide the same level or service at the same cost. As a result, it’s vital to carefully track your repair costs and service time for improvement purposes without having to replace your vehicle.
1. How Much is Your Fleet Vehicle Actually Being Used?
To understand your optimal vehicle lifecycle point, you have to figure out each unit’s utilization. While it may seem like a complex amount of information to figure out, it’s important to note that unit utilization doesn’t only tell you how much your vehicle is being used.
Reasons to track your unit utilization:
- Equipment value: Learn whether you’re getting the full value of your fleet vehicle
- Team productivity: Find out how productive your workforce is by knowing how much your vehicle runs
- Issue identification: Understand which vehicles cause problems to reduce downtime
- Cost reduction: Cut unnecessary equipment and reduce operational expenses
As you can see, unit utilization goes far beyond whether or not you should replace your vehicle. Knowing how much the trucks in your fleet are used actually help your business increase productivity, reduce expenses and decrease downtime.
When you’re busy running a warehouse where your team’s efficiency directly affects your company’s bottom line, it’s a good idea to investigate key metrics that can help you optimize the most important vehicles in your fleet.
2. Figure Out Your Vehicle’s Utilization
When you’re working on deciding whether or not you should replace a vehicle in your fleet, take some time to calculate the unit utilization of your vehicle.
You may have this information readily available, or you may have to do some digging. However, the results you get will help you determine whether your timing is right. After all, in order to get the best ROI, you should replace your vehicle at the optimal vehicle lifecycle point — not before, and not after.
If you replace your truck too early, you lose some ROI as your vehicle is still able to perform. If you wait too long, you open yourself up to additional costs that come with maintenance and repairs for older vehicles. Plus, you increase the likelihood of downtime your vehicle encounters — which lowers your productivity.
Here’s how you can track the unit utilization of each vehicle:
- Collect the Hour Meter readings on your equipment
- Build a report that compares the number of shift hours against the actual runtime
- Identify any low-utilization operators or units and see whether you can redeploy them
Tracking Your Fleet’s Usage is a Big Job
We know what you may be thinking — tracking the unit utilization looks like a complicated task you don’t have time for. We get it: your primary focus is on ensuring your warehouse operations run smoothly. You’re overseeing an entire fleet and a large staff, in charge of many supply chain elements that are time-sensitive.
But this isn’t the only thing you should be tracking in your fleet.
See How Unit Utilization Reporting Has Given Others Results
If you see the value in making important business decisions — whether or not to replace your vehicle — based on data, then it’s time you start tracking the key warehouse performance metrics that provide you with the insight you need to better run your warehouse.
To see what it’s done for Pacific Southwest Container, click here to download our case study.
Plus, Don’t Miss Our Free On-Demand Webinar
Learn what KPIs you should be tracking, how you can track them, and:
- How you can save hundreds of thousands of dollars on your fleet maintenance
- How you can avoid equipment downtime so your warehouse can run at its peak
- How to diagnose issues in your vehicles before they snowball into larger — and more expensive — problems
Watch the webinar and you’ll also get a free workbook that you can use to run your numbers, plus a cheat sheet on how to implement the 5 KPIs at your warehouse.
Interested in one of our products? Give us a call at 844-360-8217 or click below to get started with a free quote now!