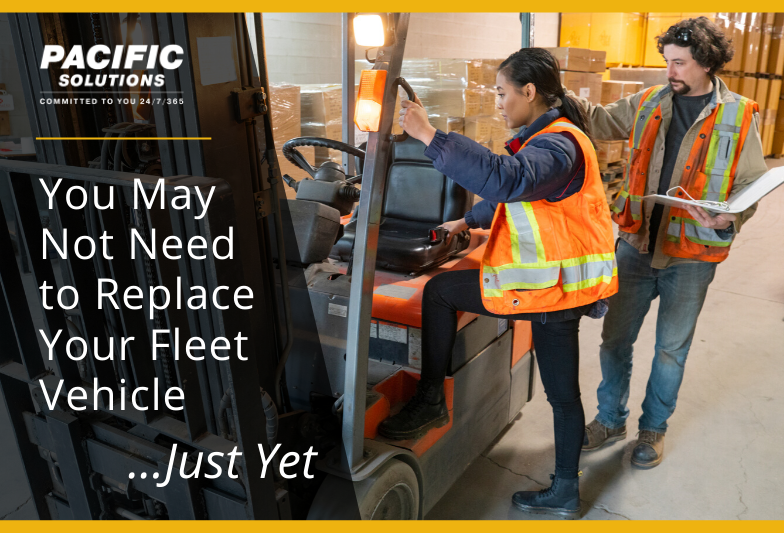
If you’re actively searching for a new material handling vehicle to replace an older one in your fleet, make sure you have all the info before you make your purchase. If you replace a vehicle too early, you risk lowering your ROI.
One of the most common reasons warehouse managers replace the trucks in their fleet is because they keep breaking down. This downtime results in a loss of productivity for the entire warehouse.
After all, your fleet vehicles do more than just help you move supplies from one place to another. They are the heartbeat of your warehouse.
Without your fleet vehicles, your business essentially comes to a literal halt.
We understand replacing a vehicle that often needs repair may seem like the best idea. You want to reduce downtime as quickly as you can, but it may not be the best financial decision for your operation. If you want to make sure you’re maximizing the ROI from each vehicle, read on.
Identify How Much Money You’re Spending on Repair and Replacement Parts
First, review the exact amount of money spent on repairs and replacement parts. Don’t estimate this number. It’s important to have an accurate account of the expenses to effectively calculate annual losses from the vehicles.
You’ll also want to find out which parts are breaking down most often.
Is it the forklift cage that keeps malfunctioning or are you always having to change the tires on your vehicle because they wear through?
Do some digging to get an idea of which parts require more money and attention.
Are You Paying for Parts Still Covered Under Warranty?
How familiar are you with the warranty coverage for the parts you’re replacing? Most clients we work with are often unaware that the parts they have been replacing — and paying for — are actually covered under warranty.
That’s just money going down the drain.
Your repair service should have this information if they are the ones purchasing the parts to repair your vehicle. However, most of them don’t have the tools and resources to keep track of which parts are under warranty.
In order to save on your repair and maintenance costs, you’ll need to take some time to research the warranties on the parts to make sure you’re not paying for things you don't need to pay for.
Find Out Why Certain Parts Wear Out Quickly — While Others Don’t
Do you have any idea of which parts wear out faster than others — and why? You may be replacing the same parts over and over on your fleet vehicle, which may make it seem that the entire vehicle should be replaced. However, it could just be a problem with the repair, the part, or the way your vehicle is being used.
Before you decide on purchasing a new vehicle or retire a new one because of repair costs, look at patterns of parts constantly breaking down. Do you notice anything that requires further investigation?
Can You Get this Data From Your Vendors?
The information that you really need to have on hand before you decide to make a new major purchase is the parts usage of each of your fleet vehicles.
When vehicles are constantly breaking down and resulting in downtime for your warehouse operations, it’s important to look into the parts that are causing all the trouble.
In a perfect world, you should be able to contact your repair and maintenance vendor and ask for the data you need:
- Which parts are being replaced most often
- How much repairs cost per vehicle
- Which parts are under warranty
- How many parts are in stock
- How quickly the parts can be delivered to your business
Unfortunately, we don’t live in a perfect world. Most vendors don’t track all of this information in detail. As a result, they can’t give you the insight you need in order to make sound business decisions.
Plus, it’s prohibitive to track all of this information on your own.
With a warehouse to run and an entire fleet and staff to oversee, you don’t have the time to backtrack through repair invoices, warranty contracts and expense spreadsheets.
Work With Experts to Get the Right Analytics
By understanding your parts usage, your warehouse can make purchasing decisions based on data to ensure you’re improving your ROI, not putting it at risk.
Some businesses keep a tab in the back of their mind for the parts they replace on a regular basis. But it takes a lot of work on your end to actually gather invoices, check warranties and get accurate information.
The mental tally isn’t accurate — and you cannot base important business decisions on that alone.
One client we worked with constantly had to replace the tires on their material handling equipment. When we looked at their parts usage report, it turned out they were running their forklift over railroad tracks that were destroying the tires. This wasn’t a problem with the tires or the forklift — it was a problem with how the vehicle was being used.
Once we corrected that, they no longer had to replace their tires — or their vehicles — as often.
Parts Usage Isn’t the Only Metric You Should Track
If you see the value in tracking parts usage, then you’ll be interested to know that there are 4 additional metrics that should be tracked, which together optimize your warehouse and help you make better business decisions — such as whether or not to replace a vehicle.
If you’ve got questions about parts usage data and how it can help you make better business decisions, don’t hesitate to get in touch with us. Call us at 844-360-8217 or book a no-obligation consultation to get started.
Interested in one of our products? Give us a call at 844-360-8217 or click below to get started with a free quote now!